Under our Body-in-White Systems Engineering division, we are a team powered by people with specialised expertise and diverse experiences who can facilitate digital manufacturing engineering solutions for automated production lines for our customers with efficient, innovative, and effective solutions that fit your needs and enable your successful automation under one roof, including everything from process planning and layout, mechanical design, and robotic simulation up to offline logic programming and online robot programming and cell alignment or data reconstruction using plant-scanned data or robot backup integration. As you know, the usage of robotics increases the efficiency, speed, and quality of the product for labour-intensive production lines, where people are performing high-volume, highly transactional process functions. This will boost their capabilities and save them money and time with robotic process automation software.
Our broad customer portfolio allows us to take on any type of project, guiding it to its goal through domain expert services of the highest quality. Our flexible delivery models are designed to scale to meet project demands where and when our clients need us. We ensure that our clients must get solutions from the top minds in the field, engineers who’ve solved critical problems for global leaders in nearly all major line builders across the globe, and we always prefer to keep all our resources updated in a rapidly changing world. Customers are the most important visitors to our premises. We are only satisfied when our customers are satisfied.
We have a highly experienced and expertized team that can provide optimised and cost-effective design solutions to our customers. Our team takes care of all aspects of manufacturing, maintenance, and safety guidelines during design. We have vast project experience with various global OEM standards. We have an international presence with a dedicated project management team in various regions to support our global customers.
We can cater to multiple solutions from a process planning point of view to find the optimum solution. So that each piece of equipment in the cell, including the robots and accessories, is effectively utilised in the best customised layout area as per factory requirements, where robots are sequenced with each other through signals, so that they can work together, sometimes in overlapping zones, while still maintaining the safety of humans and equipment. Of course, before starting, a cell is built, and tasks are assigned to these robots. A great deal of attention is paid to finding the right place in the right orientation with the right spacing between all the robots, tools, panels, and other equipment put in the cell, among many other fine considerations. While reachability and avoidance of joint lock or singularity conditions are key considerations, safety and ease of maintenance are always higher priorities. Each robot and each tool are assigned the optimum level of tasks, e.g., numbers of welds, multiple joining, and processing foolproof applications in the same line. So that the cell is well balanced, and humans and robots can finish their assigned tasks well within the required cycle time with a safety margin of time to spare.
In the end, a detailed sequence of operations is prepared, and interlocks between operations are defined. Next, these robots are run through real-time controllers (RCS) to check for their real-time behaviour; any jerky motion, any singularity lock, any unnecessary waiting, or any missing connection are carefully investigated. Only when all these are resolved, we can say that our cell is ready to upload the OLP data to integrate with the physical robots.
In brief, we have an expert team that has experience with each step of any type of robotic simulation.
Tasks, including the 2D shop floor layout planning job, by utilising various software’s as per customer demand. It starts with process planning, cell, and tooling validation, gun/EOAT selection and validation, robot path planning, work cell and operator safety consideration, ergonomics check, cable tray and utility planning, cycle time study, collision-free path creation, robot interlocks check, offline line programming, cell alignment or reconstruction, CT optimisation, etc.
Why to Sphinx?
- Technically sound team.
- Issue tracking and milestone management.
- Single point of contact for technical leads.
- Well-structured team with excellence in project management.
- Clear vision about technological know-how.
- Dedicated on-site engineering support is available in the shortest amount of time.
- Flexible with a turnkey solution or fixed-cost model solutions.
- We are always ready to provide dedicated ODC facilities to our customers for a long-term relationship.
- Enhanced communication with Teams software.
- Available with a large team size and is cost-effective relative to competitors.
- Global presence and experience with approximately . all major line-builders across the globe.
- Expert resources will reduce rework during the build phase.
- Very good team size with flexibility in hours of availability.
- Easily adapt to engineering change requirements.
- Avoid costly mistakes and delays by getting it right the first time.
- Increase productivity and maximise resource utilisation.
- Fully exploit the agility of robotic systems to optimise robot processes and provide the best engineering solutions.
- (Participation in the RFQ Study and Estimation) More than 8 lakh hours per year. Shows our strong upcoming projections.
- Familiarise yourself with multi-variant line simulation.
- Flexible to deliver the job on different software segments. Delmia, Process Simulate, and Robcad.
- Dual skill set resources are available with digital simulation as well as shop floor experience in robotic programming.
Featured Competencies:
- Cell buildup as per production requirements.
- Optimisation for Floor Space and Cycle Time.
- Safety requirements in the cell.
- Robot safety zoning and signalling.
- Robot Safety (Kuka Safe, Safe Move, Fanuc DCS).
- Offline Programming.
- Offline robot logic building with all required I/O instructions.
- Sequence of Operations.
- CEE and VC environments build facilities.
- Various body shop applications, e.g.Spot Welding, Riveting, Clinching, Flow Drill Screws, Stud/NNut.
- Welding, and VIN Marking MIG/MMAG welding, gluing/sealing, roller hemming, etc.
- BIW tooling design as per customer requirements.
- Incorporation of component changes.
- Cost-effective and feasible design solutions.
- Safety and ergonomic considerations are top.
- Carry out projects efficiently and with on-time deliveries.
- Expert Team for 3D and 2D Support.
- Almost all design documents support them (sequence sheet, clamp plan, ergo, payload, poka-yoke).
- Sphinx had designed tooling for various car parts.
- Body Side Inner Outer.
- Front door, rear door, and split door.
- Tail gate.
- Fender.
- Underbody.
- Wheelhouse.
- Hood.
- Chassis.
Also, we have working proficiency in pneumatic or manual fixtures, grippers, tackles, lift assist, conveyor pallets, takeouts, racks, buffers, platforms, frame structures, stands, etc.
Sphinx had wide experience with multiple OEM working standards in body-in-white tooling design.
VW / AUDI / SKODA
- BMW.
- FORD.
- SEAT.
- STELLANTIS / MASERATI / FCA.
- DAIMLER.
- GM.
- VOLVO.
- SCANIA.
- TESLA.
- RENAULT.
- Catia.
- NX.
- Fides.
SIMULATION SOFTWARE COMPETENCIES:
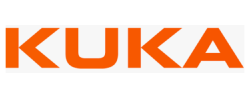
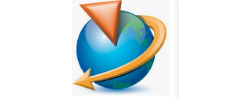
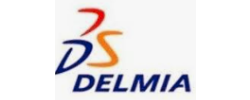
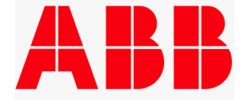
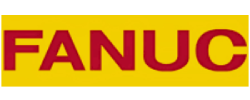
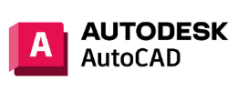